So I have one of those tiny bandsaws you can get at Menards (or home depot or lowes probably) and truthfully I’ve been impressed with it overall. Wood is no sweat, aluminum is ok however steel is out of the question. It just runs too fast, I’ve ruined a couple blades trying it. Now we could slow it down if we wanted to but why do that when you can massively overcompensate.
You’ve probably already seen the image directly above. We’re going to hack/mod this massive 100 year old Regal meat saw.
The first problem is this thing is 3 phase. All I’ve got is single phase so we’ll have to deal with that. However this is an opportunity in disguise. See a meat saw runs even faster than a wood saw with basically a continuous razor blade loop instead of a blade, kinda terrifying. We need it to run drastically slower. So the first thing we’ll do is a add a VFD. You can find an appropriate one in my store:
https://whathavewelearned.myshopify.com/collections/bandsaw
That VFD isn’t branded the same as the one I got but it looks identical. One thing to watch out for, the terminal screws are way way way too short. I wired this with 10awg stranded and with ferrules (there’s a very handy ferrule crimper in the store, you should always use these with screw terminals and stranded wire) the wire wouldn’t fit under the screw head on the terminal. I had to replace some with longer screws. Also if you drop one of the terminal screws (there’s no flat on the end to stop them from falling out) you can get them through the grill in the front of the housing meaning you have to take the thing apart to put them back in, and if you already have some wires in there you have to remove the wires first and redo everything. Or you can do what I did and butcher the grill so you can get the screws in without all that hassle.
Alright so ferrule the wires and wire them in. So for 220 (240v if you want to be pedantic) single phase you have two wires that matter, simply put the two that aren’t neutral. You may notice the terminals are labelled L and N implying line and neutral. This threw me for a moment until I realized this thing isn’t from the USA. Almost every where else has 220v on the Line wire and a neutral to return. That’s fine, whatever, just wire in the two hot wires on L and N and put your actual Neutral on the ground terminal, it’s grounded in your panel anyway. Then hook your 3 wires from your 3 phase motor to your 3 terminals. The order doesn’t matter to much although if the motor runs backwards you’ll need to swap the first and last wire. Just remember each of the three wires is connected to two of the other coils in the middle, no orientation can be wrong…. I think.
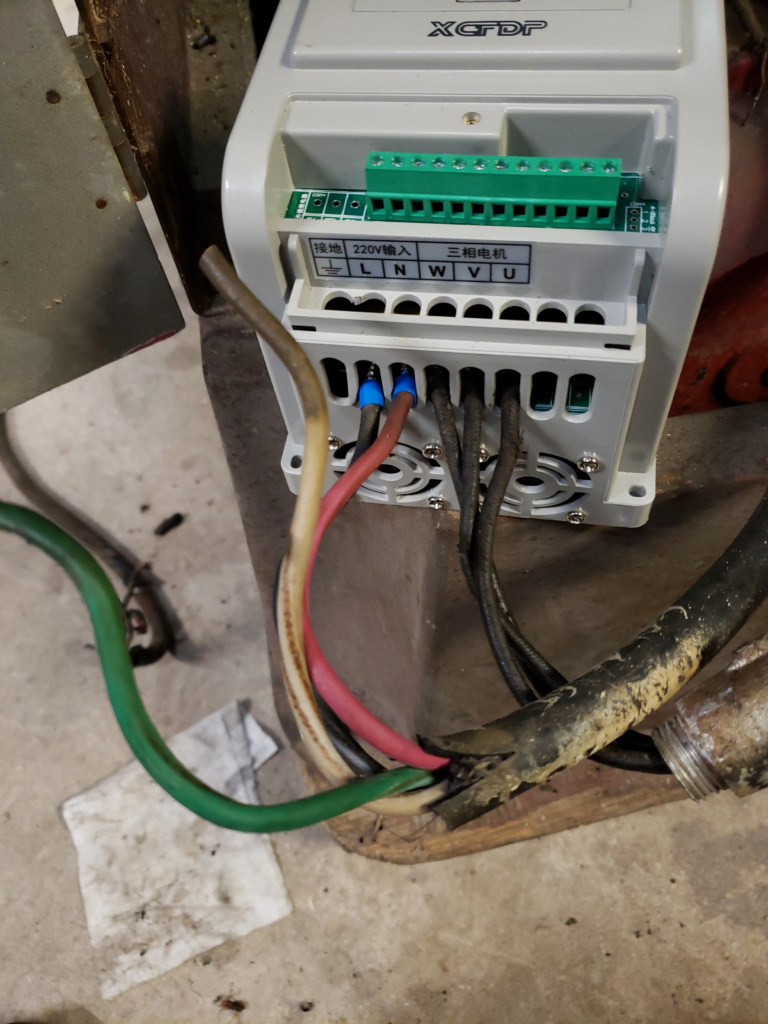
Alright, so does it work?
You better believe it.
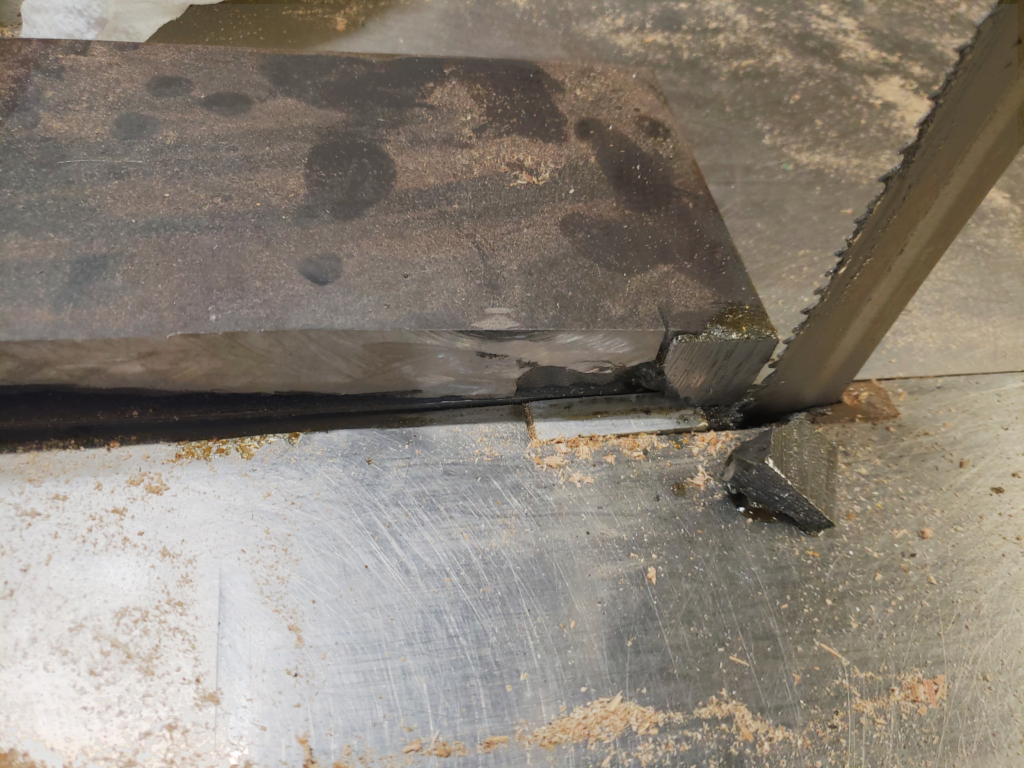
1 inch thick steel plate, no sweat. You can see I got a very aggressive tooth blade. I got that from USA Bandsaw blades.
https://www.usabandsawblades.com
I’m happy with the blades, 10ft 6in. Glad my measurements were good that was something like $150. I also got a wood cutting blade that’s much thinner than the steel blade so we can do some curvy stuff..
I mentioned I got an aggressive blade, there’s a reason for that. See this thing still isn’t technically going as slow as it should be. My understanding is for metal you really want to be somewhere near 200-300 feet per minute on your blade speed. When I slow it down to that speed with the VFD (the dial on the front changes the AC frequency) the motor stalls under minimal load. So with the more aggressive tooth count we get fewer teeth in the cut and we can run a little faster. I considered changing the pulleys around and all that and with a lathe and a mill that really shouldn’t be a huge problem but because of the way the saw is assembled that’s going to be a bigger project than I have time for now.
So the saw works but there’s more to do. Next on the list of saw projects is building custom blade guides, I want bearings on 3 sides top and bottom and the current top blade guide doesn’t come down far enough because no one uses a 7ft tall bandsaw to cut 1/4 inch thick steaks. Then I will add a coolant system. This will have wipers on the blade below the deck and some kind of catch system and an adjustable nozzle, both position and spray as well as some kind of automatic coolant cycler. I hear coolant goes bad and/or clogs if you don’t run it often enough so we’ll solve that by have a system that automatically runs the coolant for a while nightly. And lastly we will add an auto-feed system. Occasionally I may want to cut massive stock (by massive I mean 6 inches or more in diameter). Well I don’t want to stand there pushing on it for an hour while it cuts. So instead we will have a carriage (it already has a carriage conveniently kind of like a deli saw if you’ve seen those) with a motor and lead screw where you can set your feet per minute rate and push a button and it will feed the stock in at whatever rate. Should be pretty nifty.
Updates coming soon! Buy something from store! Read the disclaimer!!
3 Replies to “DIY – Lets Hack a Bandsaw”